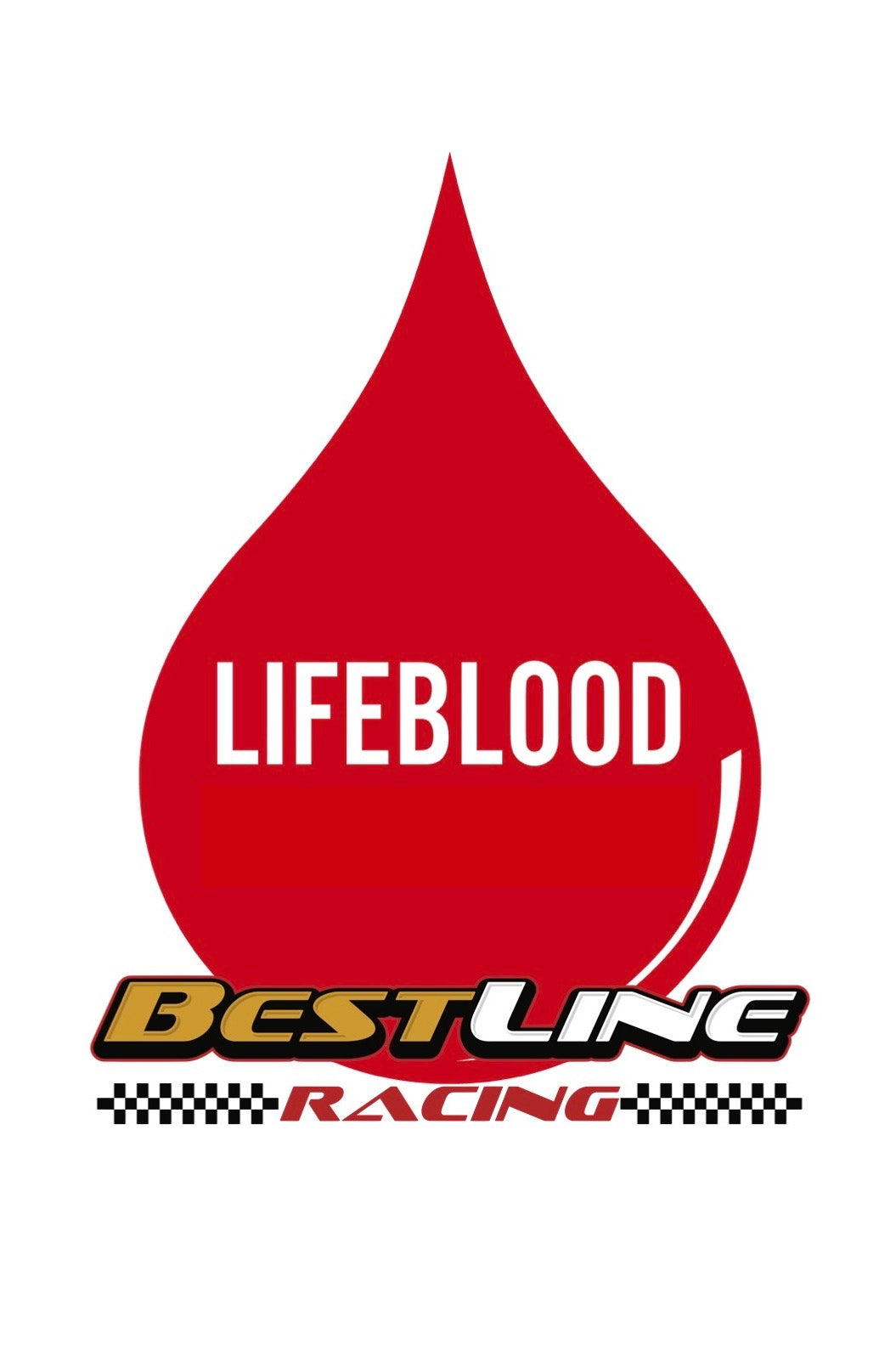
Understanding Galvanic Corrosion in Automotive Engines
Galvanic Corrosion in Automotive Engines: A Design ChallengeGalvanic corrosion poses a significant challenge for automotive engineers, particularly when it comes to engine design. As vehicles evolve to incorporate lighter materials and more complex systems, the risk of galvanic corrosion increases. This blog post explores the importance of addressing galvanic corrosion early in the design process and strategies to mitigate its effects.
Understanding Galvanic Corrosion in Automotive Engines
Galvanic corrosion occurs when two dissimilar metals come into electrical contact in the presence of an electrolyte1. In automotive engines, this can happen in various components, such as:
- Aluminum engine blocks with steel cylinder liners
- Magnesium alloy components in contact with steel fasteners
- Copper radiators connected to steel or aluminum parts
The presence of coolant, condensation, or even road salt can act as electrolytes, accelerating the corrosion process2.
Early Consideration in Design
When designing automotive engines, it's crucial to consider galvanic corrosion from the outset. This proactive approach can save manufacturers significant costs in repairs and warranty claims down the line3. Key factors to consider include:
- Material selection: Choose metals with similar electrochemical potentials to minimize galvanic effects4.
- Environmental factors: Consider the operating conditions, including temperature, humidity, and exposure to corrosive substances5.
- Component interfaces: Pay special attention to areas where dissimilar metals come into contact1.
Mitigation Strategies
While completely eliminating galvanic corrosion may be challenging, several strategies can help mitigate its effects:
- Insulation: Use non-conductive materials to separate dissimilar metals4.
- Protective coatings: Apply barrier coatings to prevent direct metal-to-metal contact6.
- Sacrificial anodes: Incorporate components designed to corrode preferentially, protecting more critical parts7.
- Drainage design: Ensure proper drainage to minimize electrolyte accumulation8.
Challenges in Implementation
It's important to note that completely isolating components from corrosive environments is often impractical in automotive design9. Engines must interface with various systems and operate in diverse environmental conditions. This reality underscores the need for innovative solutions and ongoing research in corrosion prevention.
Emerging Technologies
As the automotive industry evolves, new technologies are emerging to combat galvanic corrosion:
- Advanced coatings: Zinc-flake and fluoropolymer coatings offer excellent protection against galvanic corrosion10.
- Composite materials: Increasing use of non-metallic components can reduce galvanic corrosion risks11.
- Corrosion inhibitors: Specialized additives in engine coolants can help mitigate corrosion12.
Conclusion
Addressing galvanic corrosion in automotive engine design requires a multifaceted approach. By considering corrosion risks early in the design process and implementing appropriate mitigation strategies, manufacturers can significantly improve the longevity and reliability of their engines. As the industry continues to innovate, new materials and technologies will play a crucial role in combating this persistent challenge.
Share