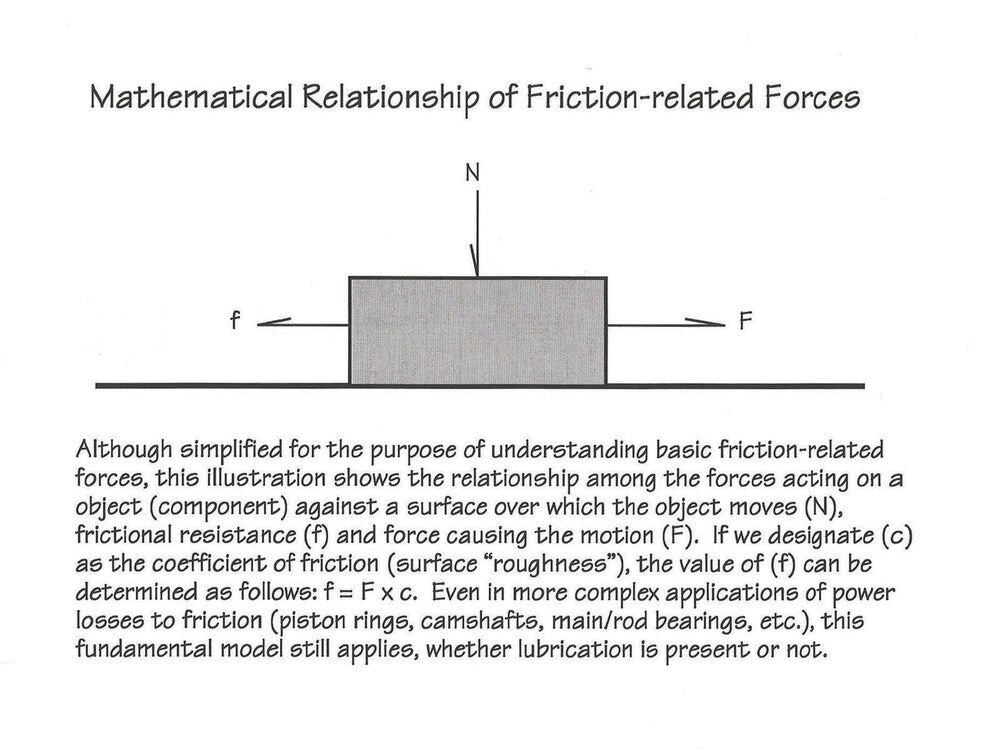
What is Friction and How to Reduce its Affects

As you would expect, there are several areas within an engine where frictional losses are created, at the very minimum. Also consistent with conventional wisdom is the fact they are unavoidable and can vary in magnitude, based upon where and to what magnitude there are causes. Some vary as a function of engine speed, others on how they are caused. And while there are certain ways to address minimization of the losses in power they can cause, it would probably be helpful to begin by discussing the types of internal engine friction. As sometimes spelled out in automotive engineering textbooks, we could list the fundamental types as follows: mechanical friction and pumping friction.
Mechanical Friction
Let's define this as being resistance against mechanical parts in an operating engine (pistons, crankshaft, camshaft, and so on) that resists the motion of these same parts. High school physics tells us that when one surface slides over another (relative motion), the resistance to this movement is theoretically a function of the force applied between them and the magnitude of the force creating the sliding motion. We've included a little sketch that illustrates that relationship. Does the relative surface finish play into this? Yes, but even in the presence of lubrication, the resistance to movement is fundamentally determined by the applied force between the two surfaces and the force creating movement. But there's more.
Absent any lubrication, if the force creating movement is held constant, a so-called "coulomb" friction is present. However, we'll not develop that concept because engines are lubricated. So, if the sliding surfaces are separated by a thin film of lubrication, "viscous" friction is observed. In this case, the resistance to motion is created by the shearing of the oil film separating the surfaces. This is where coatings and surface finish come into play, as you will read further in this discussion. More specifically, it was long believed that under the conditions of viscous friction surface finish was less critical than during coulomb friction. The coatings industry has and continues to alter that belief.
A significant amount of viscous friction in an engine takes place in areas involving bearings; e.g., connecting rods, main bearings, cam bearings, and comparable areas. Let's not overlook the viscous friction involving piston skirts. Generally, these locations experience a higher degree of viscous friction than near the ring lands where combustion temperatures can reduce the amount of available lubrication. Furthermore, if you were to sum up the frictional losses in a WOT engine, it's fair to say in excess of 75 percent of these losses are mechanical.
Piston Friction
Let's not leave piston friction losses for a moment, because there are more salient points to discuss. We mentioned that there are likely lubrication differences between the skirt and ring areas. In fact, it's generally believed that the rings operate in a coulomb friction condition. The extent of this condition is in large measure not a function of engine speed but combustion (gas) pressure. As this pressure increases (higher power levels), side-loading the piston increases correspondingly, accompanied by an increase in coulomb friction. In such cases, the viscous friction levels experienced by the piston skirt also increases since lubricant film thickness can be negatively affected.
And lest you get the impression this column is an advocate for coatings and improved surface finishes, surely you can see the potential benefits from either or both. It's probably safe to say that total piston friction (coulomb and viscous) loses are related to engine speed, all else being equal.
Pumping Friction
The summation of work performed during the inlet cycle and respective exhaust cycles is defined as "pumping friction." For example, for an inlet cycle to be initiated, cylinder pressure would need to be less than atmospheric pressure. Correspondingly, for an exhaust cycle to be initiated, cylinder pressure must be higher than atmospheric pressure. At lower engine speeds, work performed by the piston to exhaust combustion residue tends to be greater than work performed by atmospheric pressure during the inlet cycle, causing a reduction in net power. As engine speed increases, piston action tends to force out combustion residue and create a more vigorous inlet cycle as well. This causes an increase in the pressure drop across both the intake and exhaust valves, thereby increasing during the exhaust cycle and lowering it during the inlet cycle, resulting in a corresponding increase in pumping friction.
How can you measure engine friction?
One time-honored method is to motor an engine using an external power source such as an electric motor. The fundamental problem with this method is that during motoring, pressures, temperatures, and the oiling process all differ from what they are during actual engine operation. A more accurate means is to create an "indicator diagram." Although a description of this method is beyond the scope of this discussion, we will share that the process allows the computation of indicated horsepower, from which friction horsepower is then computed.
Some concluding thoughts about internal engine friction
As a practical matter, it's one thing to identify, define, and understand the elements of certain engine conditions, and it's an entirely different issue to address solutions to the problems. In this particular instance, while proper engine lubrication is vital to parts life, there are ways to control excessive lubrication that can lead to power loss; e.g., windage control, limiting upper engine lubrication, as examples. Professional engine builders have employed these techniques for decades.
However, and on a continually-evolving basis, a wide range of new lubricants and surface treatments are providing new and increasingly-affordable ways to reduce engine friction. And in many instances, controlling the operating temperatures of friction surfaces is linked directly to frictional losses in an engine. There's currently no way around the elimination of traditional friction losses, even with Diamond Nano-Lubricants that reduce as much as 60%, but it's certainly worthwhile to continue to explore the tribology being developed by the lubrication community of providers.
Share